Wenn es um den FDM-3D-Druck geht, ist der erfolgreiche Druck mit Hochtemperaturmaterialien immer noch eine der anspruchsvollsten Perspektiven.
Diese Materialien erfordern Drucktemperaturen, die oft deutlich höher sind als die von normalen FDM-Materialien wie PLA, ABS und PET-G. Hochtemperaturwerkstoffe haben oft außergewöhnliche thermomechanische und chemische Eigenschaften und sind in der Regel High-End-Anwendungen in der Luft- und Raumfahrt, der Automobilindustrie, dem Gesundheitswesen, der Forschung und der Produktion vorbehalten.
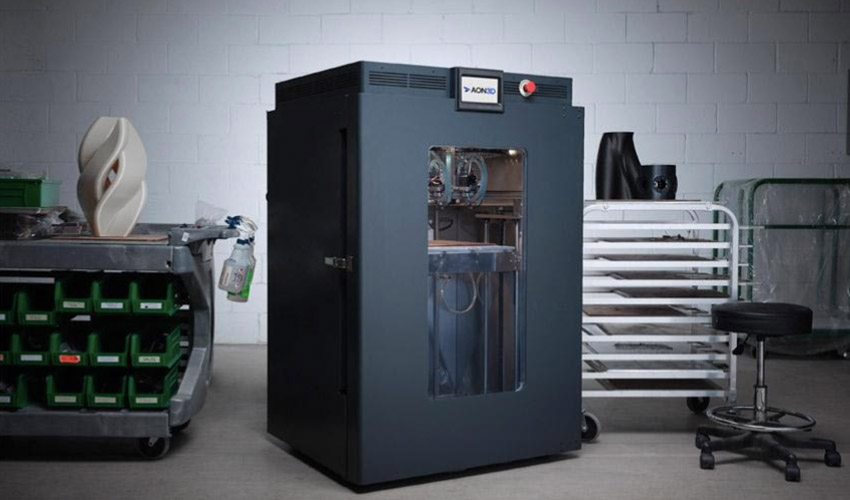
Hochtemperaturwerkstoffe
Hochtemperaturwerkstoffe werden oft als solche bezeichnet, weil sie bei hohen Temperaturen arbeiten. Dies ist häufig das Ergebnis einer festeren und starreren chemischen Struktur, die bei steigender Temperatur weniger anfällig für viskoelastische Verformungen ist. Infolgedessen behalten diese Materialien oft ihre Steifigkeit bei hohen Temperaturen, während Kunststoffe wie ABS und Nylon dazu neigen, weich und flexibel zu werden. Derzeit sind mehrere Hochtemperatur-Thermoplaste für den FDM-3D-Druck erhältlich, darunter:
PEEK
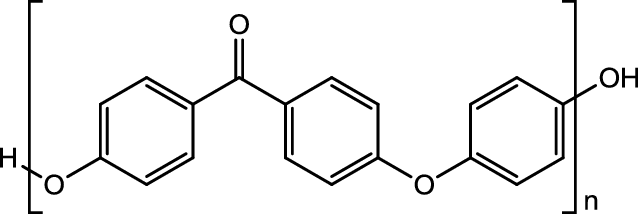
PEEK (Polyetheretherketon) ist einer der beliebtesten Hochtemperatur-FDM-Thermoplaste, da er eine Vielzahl nützlicher Eigenschaften aufweist. Es ist sehr hitzebeständig und kann seine mechanischen Eigenschaften bei Temperaturen von bis zu 260°C beibehalten. Dieses Material weist hervorragende mechanische Eigenschaften mit hohen Steifigkeits- und Zähigkeitswerten auf und ist sehr verschleißfest. Manchmal wird es sogar als Ersatz für Metallteile verwendet. Darüber hinaus weist PEEK eine ausgezeichnete chemische Beständigkeit auf und ist sterilisierbar, was seine Anwendbarkeit in medizinischen Hochleistungsanwendungen erweitert. Schließlich hat PEEK auch hervorragende dielektrische und flammhemmende Eigenschaften.
Der Nachteil ist, dass PEEK-Materialien in der Regel viel mehr kosten als andere FDM-Materialien. Da es sich bei PEEK um ein teilkristallines Material handelt, ist bei der Verarbeitung besondere Sorgfalt geboten, je nachdem, wofür das gedruckte Teil verwendet werden soll.
PEKK
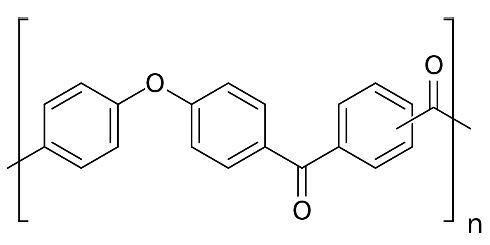
PEKK (Polyetherketonketon) ist PEEK als Material sehr ähnlich, weist jedoch einige wesentliche Unterschiede auf, die es für bestimmte Anwendungen attraktiver machen können. Obwohl die Kristallisationsgeschwindigkeit von PEKK durch Veränderung der Molekularstruktur des Materials während der Synthese gesteuert werden kann, neigt PEKK im Allgemeinen zu einer langsameren Kristallisationsgeschwindigkeit und kann daher leichter als amorphes Material verarbeitet werden. Infolgedessen neigt PEKK zu einer besseren Schichthaftung und geringeren Verformung als PEEK.
PEKK hat auch ein breiteres Verarbeitungsfenster und kann daher auf einer größeren Anzahl von Maschinen gedruckt werden, die aufgrund höherer Temperaturanforderungen möglicherweise nicht in der Lage sind, PEEK zu bedrucken. PEKK weist nicht nur vergleichbare mechanische und chemische Eigenschaften wie PEEK auf, sondern bietet auch eine höhere Festigkeit bei Druckbelastungen und eine höhere Wärmebeständigkeit als PEEK.
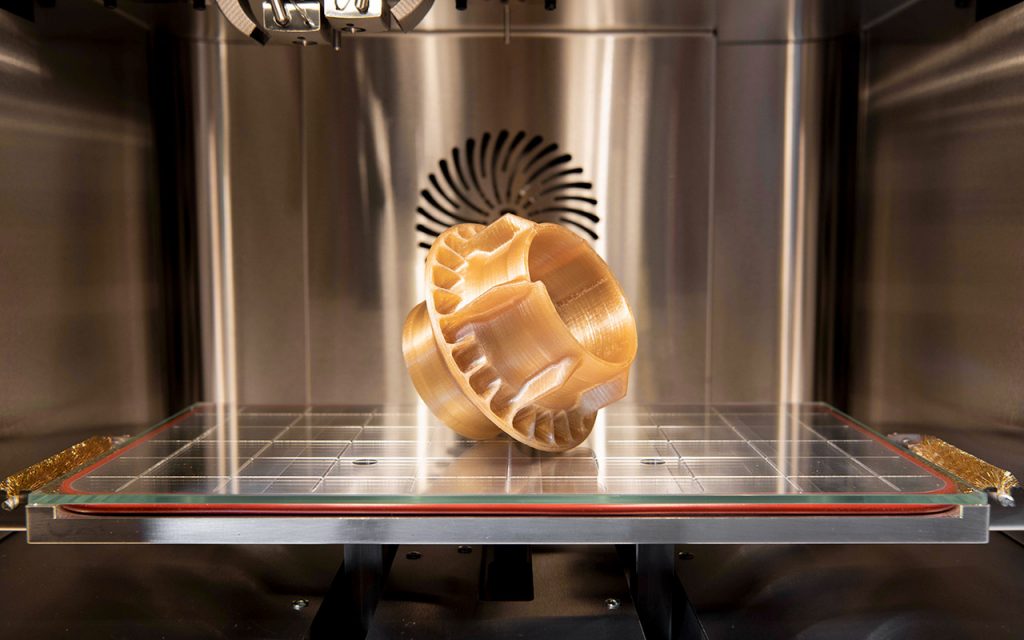
ULTEM 1010 und 9085
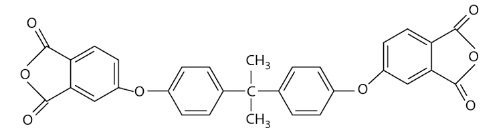
ULTEM ist der Markenname für PEI (Polyetherimid), ein von SABIC hergestelltes Hochleistungsfilament. PEI bietet ähnliche, wenn auch etwas schlechtere Eigenschaften als PEEK zu einem deutlich niedrigeren Preis. Beide Werkstoffe zeichnen sich durch außergewöhnliche chemische Beständigkeit, Festigkeit und Steifigkeit, langfristige Wärmebeständigkeit, Ermüdungsfestigkeit und Maßhaltigkeit aus. Im Gegensatz zu PEEK ist ULTEM jedoch ein amorphes Material und weist daher tendenziell eine geringere Hitzebeständigkeit auf, obwohl es eine Glasübergangstemperatur von etwa 210 °C hat (ULTEM 1010).
Wie PEEK kann auch ULTEM 1010 sterilisiert werden und ist autoklavierbar. Einige Sorten sind auch biokompatibel und für die Verwendung in Lebensmitteln zugelassen. Darüber hinaus weist ULTEM 1010 eine ausgezeichnete Chemikalien- und Wärmebeständigkeit auf.
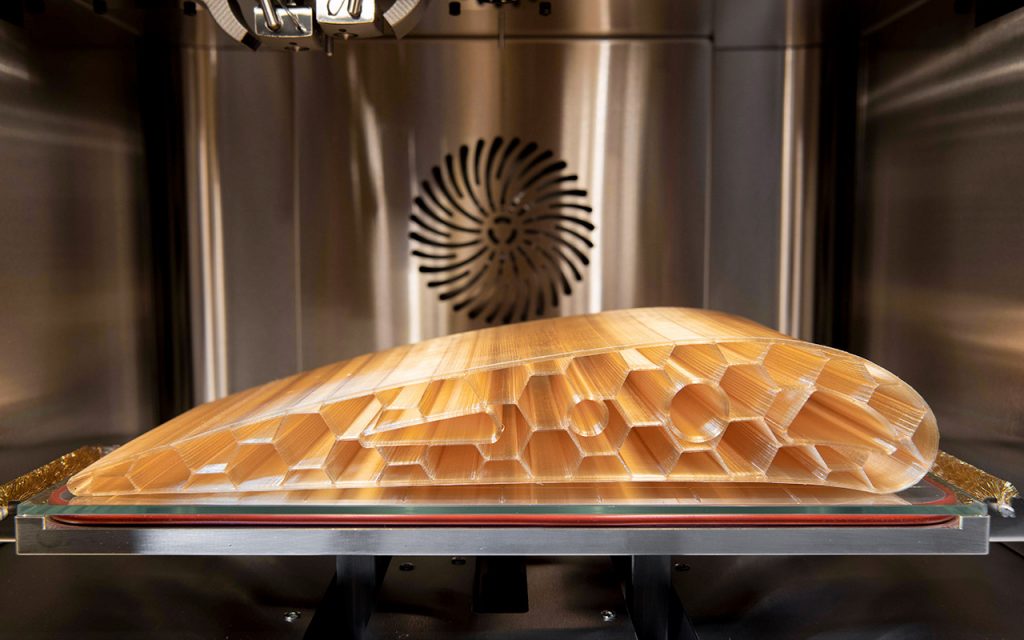
ULTEM 9085 ist eine weitere Version des von SABIC hergestellten ULTEM-Harzes, die für den FDM-Druck verfügbar ist. Auf den ersten Blick bietet ULTEM 9085 eine geringere chemische Beständigkeit und thermomechanische Eigenschaften als ULTEM 1010. Tatsächlich hat ULTEM 9085 eine HDT von etwa 153 °C, die etwa 50 °C niedriger ist als die von ULTEM 1010. Außerdem hat ULTEM 9085 eine geringere Festigkeit und Steifigkeit als ULTEM 1010, obwohl ersteres Material dadurch nachsichtiger ist als letzteres. Andererseits bietet ULTEM 9085 im Vergleich zu ULTEM 1010 eine deutlich höhere Zähigkeit und Schlagfestigkeit.
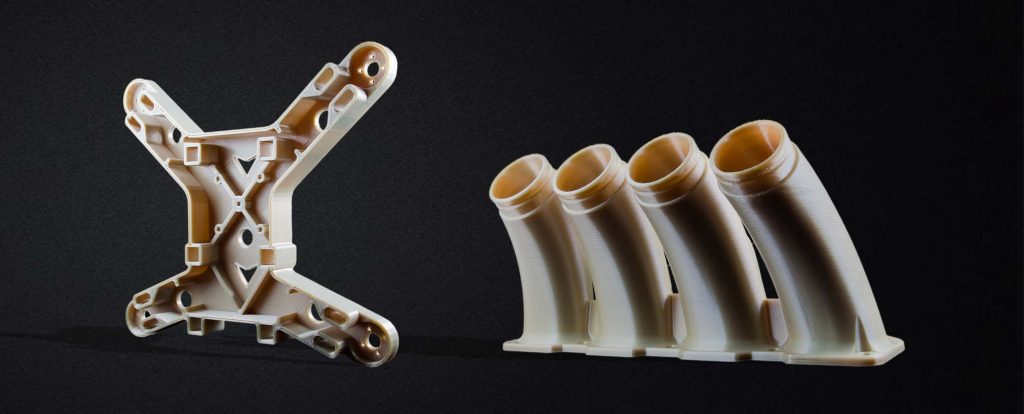
PPSU / PPSF

PPSU / PPSF (Polyphenylsulfon) ist ein Hochleistungsfilament aus der PSU (Polysulfon) Familie. Polysulfone sind Polymere, die eine Sulfonylgruppe (O = S = O) in ihrer Wiederholungseinheit enthalten. Diese Thermoplaste werden häufig in speziellen Anwendungen als besserer Ersatz für Polycarbonate verwendet. Andere Polymere aus dieser Familie sind PSU (Polysulfon), PPS (Polyphenylsulfid) und Poly-PSF (Bisphenol-A-Sulfon).
PPSU ist ein amorpher Werkstoff mit einer sehr hohen Glasübergangstemperatur (> 230°C) und einer Wärmeformbeständigkeit von ca. 190°C, wodurch er sich ideal für Hochtemperaturanwendungen eignet. PPSU hat normalerweise eine hohe Betriebstemperatur (180°C), sehr hohe Schlagfestigkeit und hohe Formstabilität. Der Thermoplast weist zudem eine sehr gute chemische Verträglichkeit und hohe Hydrolysebeständigkeit auf. Interessanterweise weist PPSU auch eine sehr hohe Beständigkeit gegenüber Gammastrahlung auf und kann sowohl im Autoklaven als auch durch Bestrahlung sterilisiert werden.
PVDF
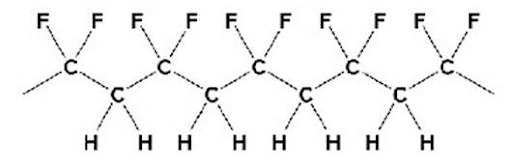
PVDF (Polyvinyldene Flouride) ist ein hochgradig inerter Thermoplast, der mit PTFE (Teflon) verwandt ist. Die Fluoratome sind in der Floupolymerstruktur sehr eng an Kohlenstoffatome gebunden, was zu der hervorragenden chemischen und thermischen Beständigkeit dieses Polymers führt. PVDF ist mit einer Vielzahl von Chemikalien kompatibel, darunter Öl, Gas und Schmiermittel sowie Halogenkohlenwasserstoffe, Alkohole, Säuren und Basen. Darüber hinaus ist PVDF widerstandsfähig gegen Kernstrahlung und sehr resistent gegen UV- und Gammastrahlung sowie Oxidation. PVDF weist außerdem eine hohe mechanische Festigkeit auf und kann bei Temperaturen von bis zu 150 °C kontinuierlich eingesetzt werden.
Tabelle 1: Typische mechanische Eigenschaften von Hochtemperatur-Druckmaterialien, Quelle: 3dxtech.com
Material | Festigkeit (MPa) | Elastizitätsmodul (MPa) | Dehnung (%) | Biegefestigkeit (MPa) | Biegemodul (MPa) | Tg (° C) | HDT (° C) |
PEEK | 100 | 3270 | 28 | 130 | 2700 | 143 | 140 |
PEKK | 105 | 3200 | 10 | 134 | 2900 | 164 | 182 |
ULTEM 1010 | 56 | 2500 | 3 | 110 | 2510 | 217 | 208 |
ULTEM 9085 | 54 | 2050 | 3 | 90 | 2170 | 186 | 158 |
PPSU | 55 | 2310 | 3 | 110 | 2215 | 230 | 190 |
PVDF | 51 | 2450 | 25 | 50 | 1800 | 170 | 158 |
3D-Druck von Hochtemperaturmaterialien
Da alle diese Materialien einen hohen Schmelzpunkt und hohe Glasübergangstemperaturen haben, sind für einen erfolgreichen Druck meist spezielle Hochtemperaturdrucker erforderlich. Die folgende Tabelle zeigt typische Druckbedingungen, die für den Druck verschiedener Hochtemperaturmaterialien erforderlich sind. Diese Werte spiegeln allgemeine Empfehlungen für den Druck von Hochtemperaturmaterialien wider. Die Druckbedingungen hängen jedoch stark von anderen Faktoren wie dem Drucker, dem Material, der Größe und der Geometrie des Teils und auch von den erwarteten mechanischen Eigenschaften des gedruckten Teils ab, wie weiter unten erläutert wird.
Tabelle 2: Typische Druckbedingungen für Hochtemperatur-Druckmaterialien
Material | Düse (° C) | Bauplatte (° C) | Kammer (° C) |
PEEK | 380-420 | 120-160 | > 90 |
PEKK | 365-400 | 120-150 | > 90 |
ULTEM 1010 | 380-420 | > 150 | > 120 |
ULTEM 9085 | 365-385 | > 140 | > 90 |
PPSU | 380-420 | > 150 | > 120 |
PVDF | 250-280 | 70-110 | / |
Beheizte Kammer
Eine aktiv beheizte Baukammer ist eine unabdingbare Voraussetzung für das Drucken von Teilen mittlerer Größe mit den meisten Hochtemperaturmaterialien. Aufgrund ihrer hohen Schmelzpunkte und Glasübergangstemperaturen führt das Bedrucken von Hochtemperaturmaterialien bei Raumtemperatur zu einer schlechten Schichthaftung und damit zu einer Schwächung der Teile. Darüber hinaus trägt eine beheizte Kammer nicht nur zu einer maximalen Z-Festigkeit bei, sondern auch zur Verringerung der inneren Spannungen und zur Begrenzung der Verformung während des Drucks. Eine beheizte Kammer trägt auch dazu bei, die Chancen auf erfolgreiche Drucke für größere Teile zu erhöhen.
Kristallinität
Da teilkristalline Materialien wie PEEK und PEKK teilkristallin sind, kann die Gesamtkristallinität eines Formteils durch Steuerung der Abkühlgeschwindigkeit des extrudierten Materials kontrolliert werden. Eine langsame Abkühlungsgeschwindigkeit begünstigt die Bildung von kristallinen Bereichen in einem Material. Andererseits neigen Teile, die schnell abgekühlt werden, dazu, einen amorphen Kunststoff zu bilden.
Amorphe Teile weisen in der Regel eine geringere Chemikalien-, Ermüdungs- und Verschleißbeständigkeit auf, haben aber bessere Haftungseigenschaften und lassen sich gut umformen. Andererseits weisen kristalline Teile in der Regel eine höhere Festigkeit, Verschleißfestigkeit und chemische Beständigkeit auf, wenn auch mit schlechteren Verbindungseigenschaften. Schließlich sind amorphe Materialien eher transparent, während kristalline Teile eher undurchsichtig sind.
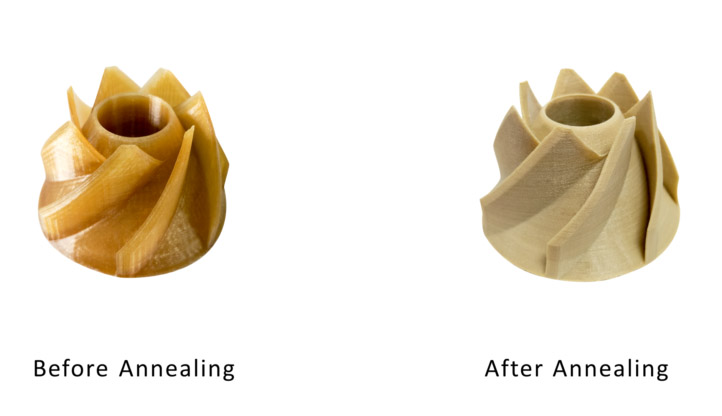
Trocknen der Filamente
Die meisten Hochtemperaturmaterialien neigen auch dazu, Wasser zu absorbieren, wenn sie einer feuchten Umgebung ausgesetzt sind. Daher muss besonders darauf geachtet werden, dass die Filamente ordnungsgemäß gelagert und bei Bedarf vollständig getrocknet werden. Filamente, die Wasser absorbiert haben, neigen dazu, Teile mit schlechteren mechanischen und ästhetischen Eigenschaften zu produzieren.
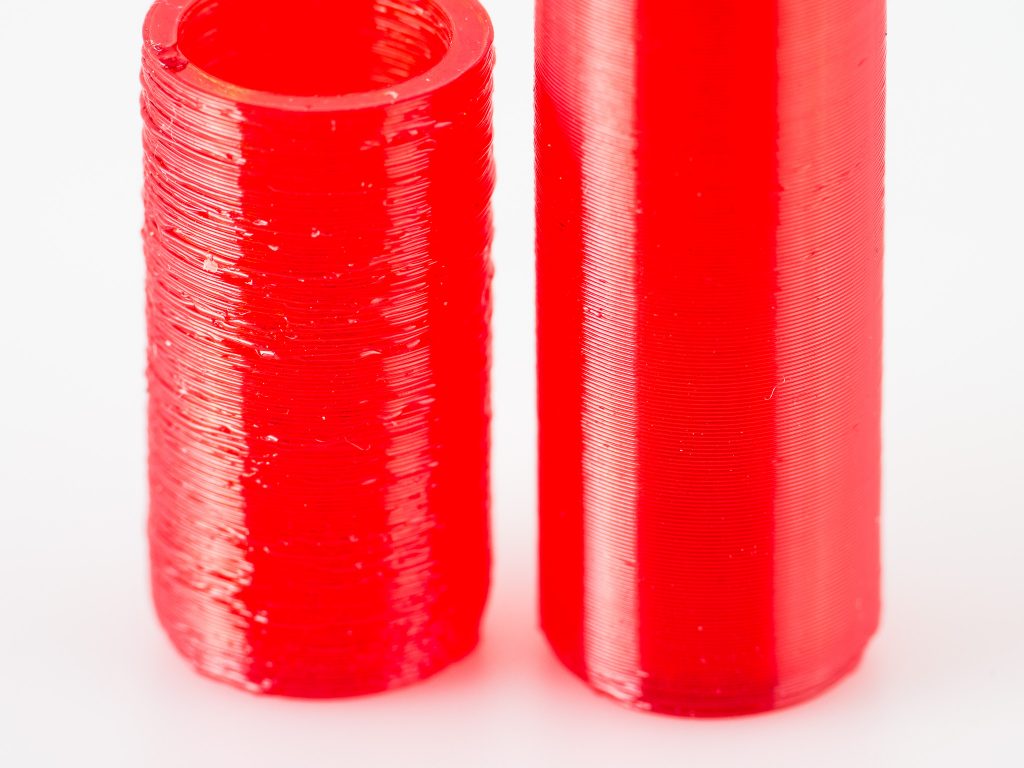
Glühen
Teile, die mit Hochtemperaturwerkstoffen gedruckt werden, könnten von einer Glühbehandlung erheblich profitieren. Bei diesem Verfahren wird das Teil auf eine bestimmte Temperatur erhitzt und dann kontrolliert abgekühlt. Das Glühen dient dazu, innere Spannungen in amorphen Kunststoffen abzubauen, vor allem aber kann es die Kristallinität in teilkristallinen Werkstoffen drastisch erhöhen, was zu besseren mechanischen Eigenschaften führt. Dies ist besonders wichtig für Materialien wie PEEK, die manchmal im amorphen Zustand geformt werden, da dies eine bessere Schichthaftung fördert. Daher werden die Teile getempert, um die Kristallinität zu erhöhen, da direkt im kristallinen Zustand gedruckte Teile zu einer schlechten Schichthaftung neigen.
Erste Adhäsionsschicht

Impressum @magigoo. com