When it comes to FDM 3D printing, successful printing with high-temperature materials is still one of the most demanding prospects.
These materials require printing temperatures that are often significantly higher than those of normal FDM materials such as PLA, ABS, and PET-G. High-temperature materials often have exceptional thermo-mechanical and chemical properties and are usually reserved for high-end applications in aerospace, automotive, healthcare, research and manufacturing
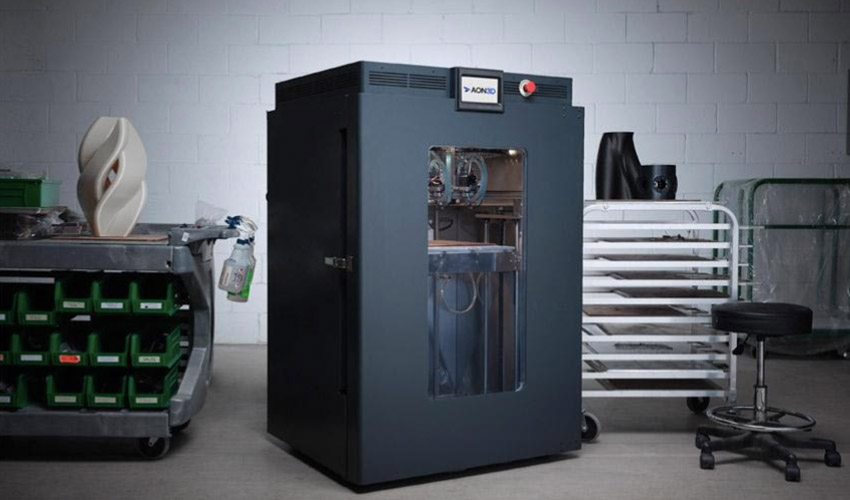
High-temperature materials
High-temperature materials are often referred to as such because of their high-temperature performance. This is often the result of a stronger and stiffer chemical structure that is less susceptible to viscoelastic deformation as temperature increases. As a result, these materials often retain their stiffness at elevated temperatures, where plastics such as ABS and nylon tend to become soft and pliable. Several high-temperature thermoplastic materials are currently available for FDM 3D printing, including:
PEEK
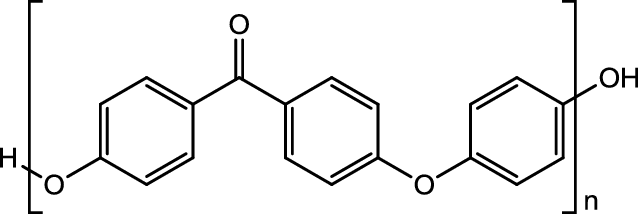
PEEK (Polyether ether ketone) is one of the most popular high temperature thermoplastic FDM as it has a vast number of useful properties. It is highly heat resistant and can maintain its mechanical properties at temperatures near 260°C. This material exhibits excellent mechanical properties with high stiffness and toughness values and is highly wear resistant. In fact, it is sometimes used to replace metal components. In addition, PEEK also shows excellent chemical resistance and is sterilizable, which broadens its applicability in high-performance medical applications. Finally, PEEK also has excellent dielectric and flame-retardant properties.
The "downside" is that PEEK materials tend to cost much more than other FDM materials. In addition, PEEK, being a semi-crystalline material, requires special care when processing this material depending on the intended application of the printed part.
PEKK
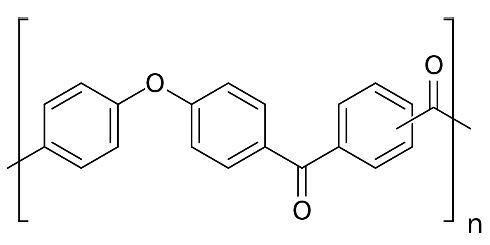
PEKK (Polyether ketone ketone) is very similar to PEEK as a material however it has some key differences that could make it more attractive for certain applications. Although the crystallization rate of PEKK can be controlled by altering the molecular structure of the material during synthesis, PEKK generally tends to have a slower crystallization rate and thus can be more easily processed as an amorphous material. As a result, PEKK tends to exhibit better layer adhesion and less deformation than PEEK.
PEKK also tends to have a wider window of processing capability and thus can be printed on a wider range of machines that may not be able to print PEEK due to higher temperature requirements. In addition, besides exhibiting mechanical and chemical properties comparable to PEEK, PEKK also offers superior strength under compressive loads and higher heat resistance than PEEK.
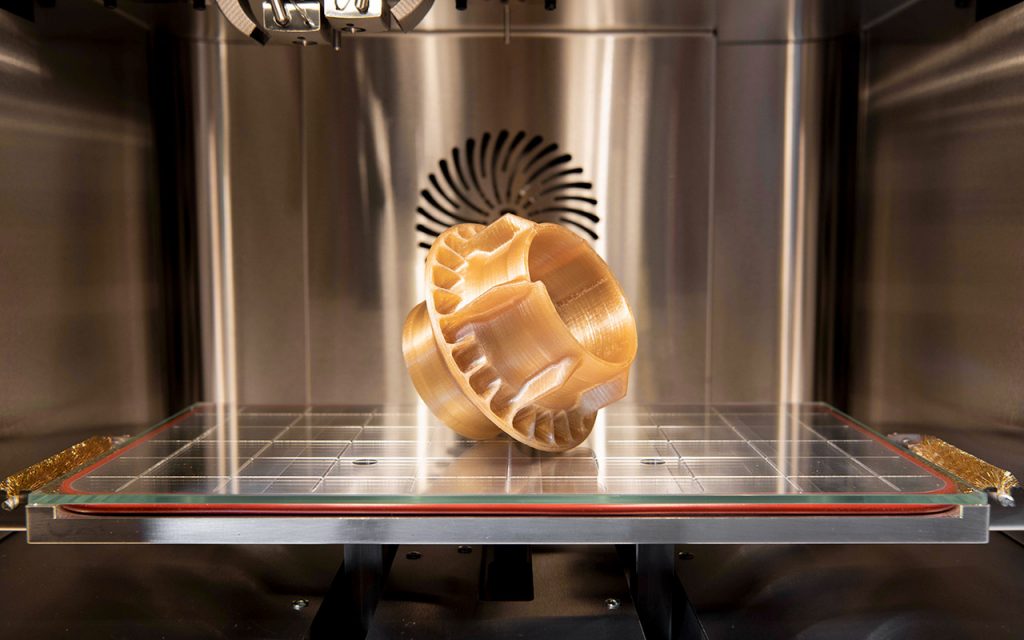
ULTEM 1010 and 9085
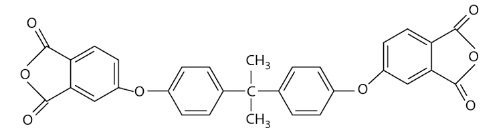
ULTEM is the brand name for PEI (Polyetherimide), a high-performance filament produced by SABIC. PEI offers similar, though slightly inferior, properties to PEEK at a significantly lower price. Indeed, both materials exhibit exceptional chemical resistance, strength and stiffness, long-term heat resistance, fatigue resistance, and dimensional stability. However, unlike PEEK, ULTEM is an amorphous material and therefore tends to exhibit lower heat resistance, even though it has a glass transition temperature of about 210°C (ULTEM 1010).
Similar to PEEK, ULTEM 1010 can also be sterilized and is autoclavable. Some grades are also biocompatible and certified for food use. In addition, ULTEM 1010 shows excellent chemical and heat resistance.
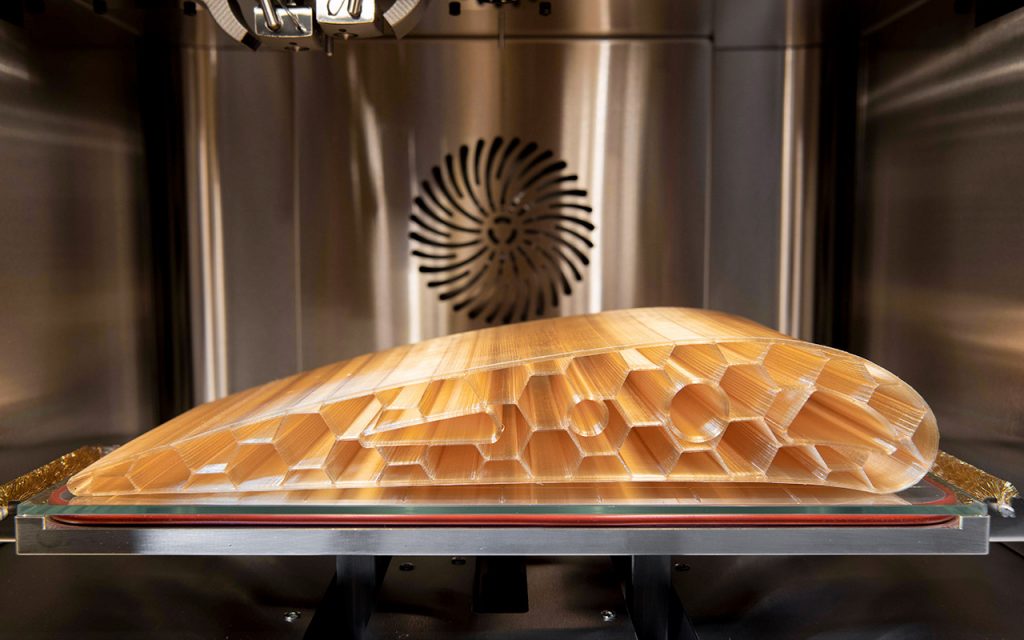
ULTEM 9085 is another version of ULTEM resin produced by SABIC available for FDM printing. At first glance, ULTEM 9085 offers lower chemical resistance and thermomechanical properties than ULTEM 1010. In fact, ULTEM 9085 has an HDT of about 153°C which is about 50°C lower than that of ULTEM 1010. In addition, ULTEM 9085 has lower strength and stiffness than ULTEM 1010, although this makes the former material more forgiving than the latter. On the other hand, ULTEM 9085 offers significantly increased toughness and impact resistance compared to ULTEM 1010.
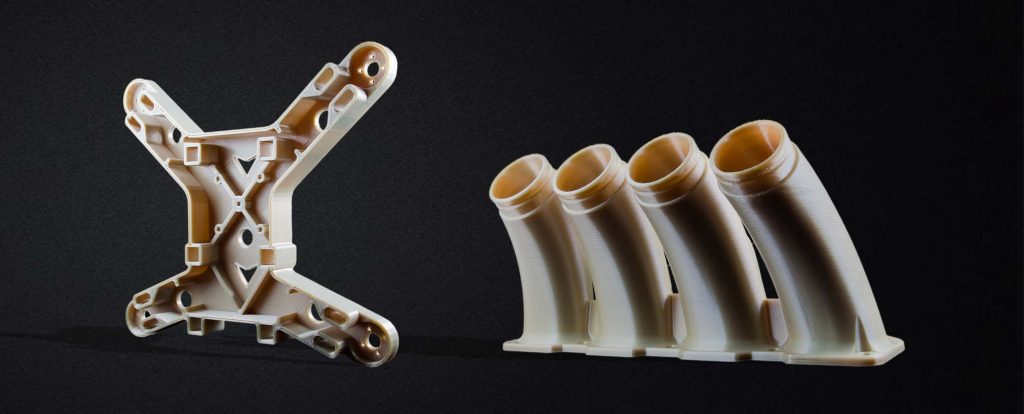
PPSU / PPSF

PPSU / PPSF (Polyphenylsulfone) is a high-performance filament from the PSU (Polysulfone) family. Polysulfones describe polymers containing a sulfonyl moiety (O = S = O) in their repeating unit. These often-used thermoplastics are often used in special applications as a superior substitute for polycarbonates. Other polymers in the same family include PSU (polysulfone), PPS (polyphenyl sulfide) and poly-PSF (bisphenol-A sulfone).
PPSU is an amorphous material with a very high glass transition temperature (> 230°C) and a heat deflection temperature around 190°C, making it ideal for high-temperature applications. PPSU typically has a high operating temperature (180°C), very high impact resistance and high dimensional stability. The thermoplastic also shows very good chemical compatibility and high resistance to hydrolysis. Interestingly, PPSU also shows very high resistance to gamma radiation and can be sterilized using both autoclave and radiation techniques.
PVDF
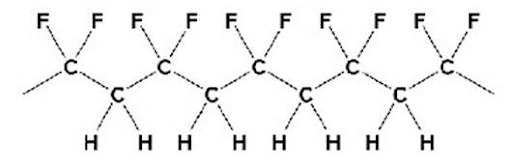
PVDF (Polyvinyldene Flouride) is highly inert thermoplastic related to PTFE (Teflon). Fluorine atoms are very closely bonded to carbon atoms in the floupolymer structure leading to the outstanding chemical and thermal resistance of this polymer. PVDF is compatible with a wide range of chemicals, including oil, gas and lubricants, as well as halogenated hydrocarbons, alcohols, acids and bases. In addition, PVDF can withstand nuclear radiation and is highly resistant to UV, gamma radiation and oxidation. PVDF also shows high mechanical strength and can be used continuously at temperatures up to 150°C.
Table 1: Typical mechanical properties of high-temperature printing materials, source: 3dxtech.com
Material | Strength (MPa) | Modulus (MPa) | Elongation (%) | Flexural strength (MPa) | Flexural modulus (MPa) | Tg (° C) | HDT (° C) |
PEEK | 100 | 3270 | 28 | 130 | 2700 | 143 | 140 |
PEKK | 105 | 3200 | 10 | 134 | 2900 | 164 | 182 |
ULTEM 1010 | 56 | 2500 | 3 | 110 | 2510 | 217 | 208 |
ULTEM 9085 | 54 | 2050 | 3 | 90 | 2170 | 186 | 158 |
PPSU | 55 | 2310 | 3 | 110 | 2215 | 230 | 190 |
PVDF | 51 | 2450 | 25 | 50 | 1800 | 170 | 158 |
3D printing of high-temperature materials
Since all of these materials have a high melting point and high glass transition temperatures, specialized high-temperature printers are most often required for successful printing. The following table shows typical printing conditions required for printing various high-temperature materials. These values reflect general recommendations for printing high-temperature materials. However, the printing conditions will strongly depend on other factors such as the printer, the material, the size and geometry of the part, and also the expected mechanical properties of the printed part, as discussed below.
Table 2: Typical printing conditions of high-temperature printing materials
Material | Nozzle (° C) | Build plate (° C) | Chamber (° C) |
PEEK | 380-420 | 120-160 | > 90 |
PEKK | 365-400 | 120-150 | > 90 |
ULTEM 1010 | 380-420 | > 150 | > 120 |
ULTEM 9085 | 365-385 | > 140 | > 90 |
PPSU | 380-420 | > 150 | > 120 |
PVDF | 250-280 | 70-110 | / |
Heated Chamber
An actively heated build chamber is an absolute requirement for printing modest-sized parts with most high-temperature materials. As a result of their high melting points and glass transition temperatures, printing high-temperature materials at room temperature will lead to poor layer adhesion resulting in weakened parts. In addition, a heated chamber will not only help ensure maximum Z-strength, but will also help reduce internal stresses and limit deformation during printing. A heated chamber also helps increase the chances of successful prints for larger parts.
Crystallinity
Semi-crystalline materials such as PEEK and PEKK are semi-crystalline; the total crystallinity of a printed part can be controlled by controlling the cooling rate of the extruded material. A slow cooling rate promotes the formation of crystalline regions within a material. On the other hand, parts that are cooled rapidly tend to form an amorphous plastic.
Amorphous parts tend to have lower chemical, fatigue and wear resistance, but have better adhesion characteristics and good forming ability. On the other hand, crystalline parts tend to show superior strength, wear resistance and chemical resistance, although with inferior bonding characteristics. Finally, amorphous materials tend to be transparent while crystalline parts tend to be opaque.
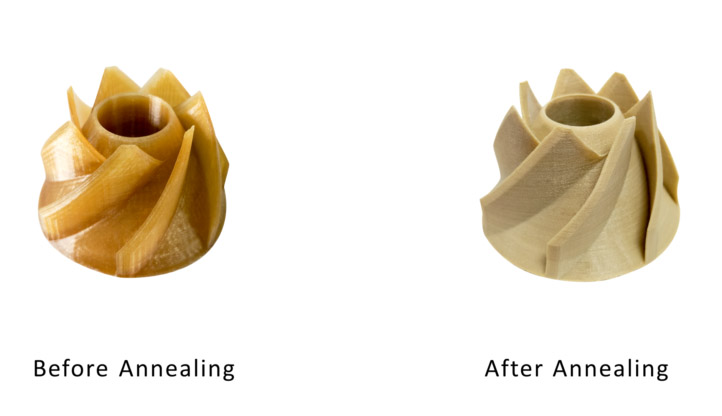
Drying the filaments
Most high-temperature materials also tend to absorb water when exposed to a humid environment. Therefore, special care must be taken to store filaments properly and to dry them completely when necessary. Filaments that have absorbed water tend to produce parts with inferior mechanical and aesthetic properties.
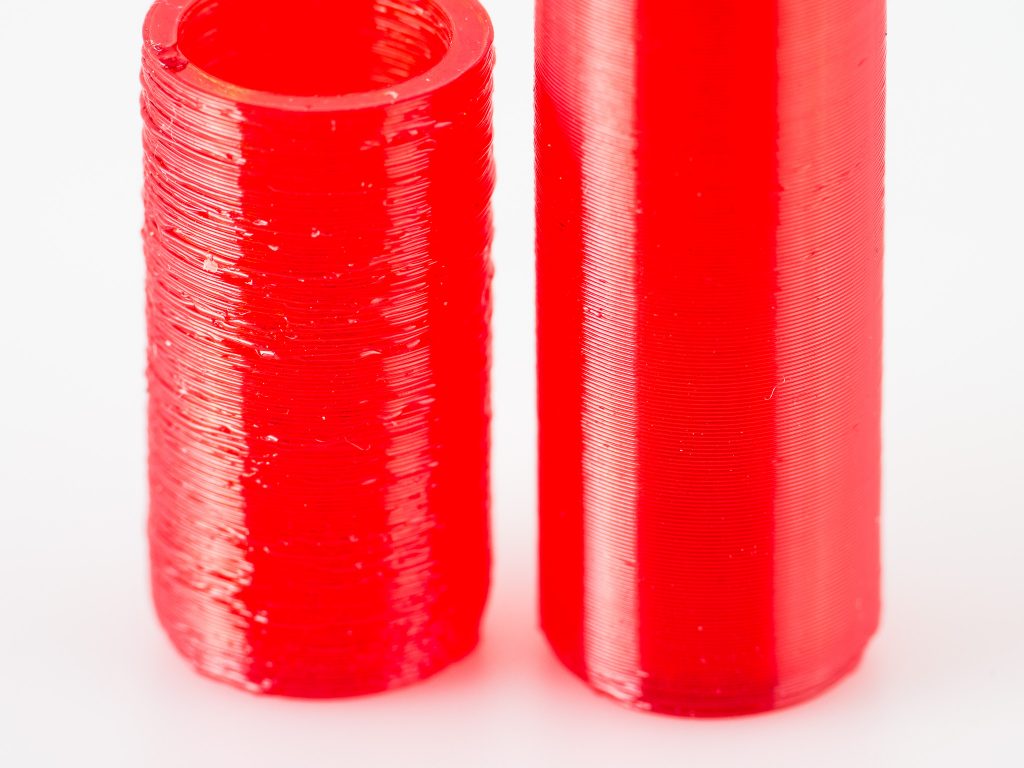
Annealing
Parts printed with high-temperature materials could benefit significantly from annealing. This process involves heating the part to a specified temperature and then cooling it at a controlled rate. Annealing serves to relieve internal stresses in amorphous plastics, but more importantly it can dramatically increase crystallinity in semi-crystalline materials leading to improved mechanical properties. This is especially significant for materials such as PEEK that are sometimes molded in the amorphous state, as this promotes greater layer adhesion. So parts are annealed to increase crystallinity, since parts printed directly in the crystalline state tend to show poor layer adhesion.
First adhesion layer

Credits @magigoo.com