Cuando se trata de la impresión 3D FDM, el éxito de la impresión con materiales de alta temperatura sigue siendo una de las perspectivas más exigentes.
Estos materiales requieren temperaturas de impresión que suelen ser considerablemente más altas que las de los materiales FDM normales, como el PLA, el ABS y el PET-G. Los materiales de alta temperatura suelen tener propiedades termomecánicas y químicas excepcionales y suelen reservarse para aplicaciones de alta gama en los sectores aeroespacial, automovilístico, sanitario, de investigación y de producción.
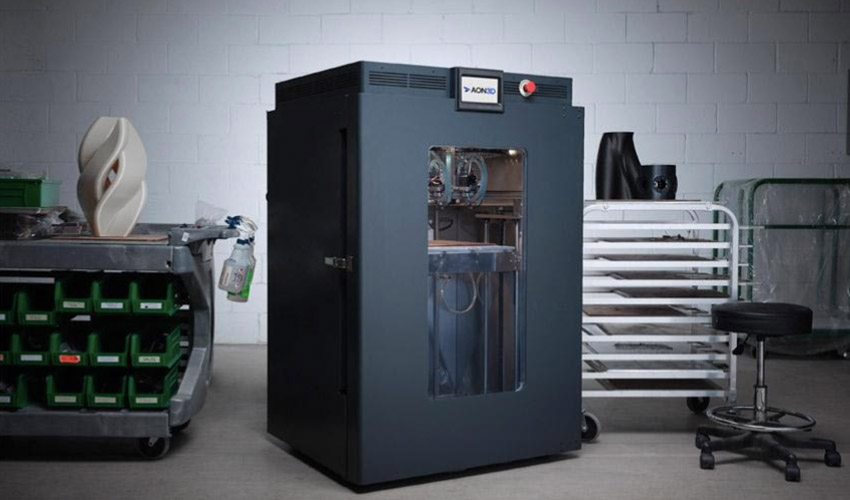
Materiales de alta temperatura
Los materiales de alta temperatura suelen denominarse así por su rendimiento a altas temperaturas. Esto suele ser el resultado de una estructura química más fuerte y rígida que es menos susceptible a la deformación viscoelástica al aumentar la temperatura. Por ello, estos materiales suelen conservar su rigidez a temperaturas elevadas, mientras que los plásticos como el ABS y el nailon tienden a volverse blandos y flexibles. En la actualidad existen varios termoplásticos de alta temperatura para la impresión 3D FDM, entre ellos:
PEEK
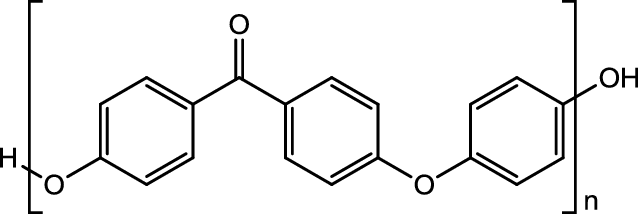
El PEEK (poliéter éter cetona) es uno de los termoplásticos FDM de alta temperatura más populares, ya que tiene un gran número de propiedades útiles. Es muy resistente al calor y puede conservar sus propiedades mecánicas a temperaturas cercanas a los 260 °C. Este material presenta excelentes propiedades mecánicas con altos valores de rigidez y tenacidad y es muy resistente al desgaste. De hecho, a veces se utiliza para sustituir componentes metálicos. Además, el PEEK también muestra una excelente resistencia química y es esterilizable, lo que amplía su aplicabilidad en las aplicaciones médicas de alto rendimiento. Por último, el PEEK también tiene excelentes propiedades dieléctricas y retardantes de la llama.
El "inconveniente" es que los materiales de PEEK suelen costar mucho más que otros materiales de FDM. Además, el PEEK, al ser un material semicristalino, requiere un cuidado especial a la hora de procesar este material en función de la aplicación prevista de la pieza impresa.
PEKK
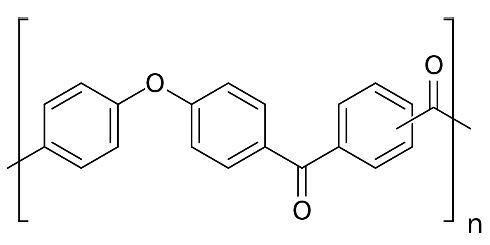
El PEKK (poliéter cetona cetona) es un material muy similar al PEEK, pero tiene algunas diferencias clave que pueden hacerlo más atractivo para determinadas aplicaciones. Aunque la velocidad de cristalización del PEKK puede controlarse alterando la estructura molecular del material durante la síntesis, el PEKK suele tener una velocidad de cristalización más lenta y, por tanto, puede procesarse más fácilmente como material amorfo. Como resultado, el PEKK tiende a mostrar una mejor adhesión de las capas y una menor deformación que el PEEK.
El PEKK también tiende a tener una ventana más amplia de capacidad de procesamiento y, por lo tanto, puede imprimirse en una gama más amplia de máquinas que tal vez no puedan imprimir PEEK debido a los requisitos de temperatura más altos. Además de presentar unas propiedades mecánicas y químicas comparables a las del PEEK, el PEKK también ofrece una resistencia superior bajo cargas de compresión y una mayor resistencia al calor que el PEEK.
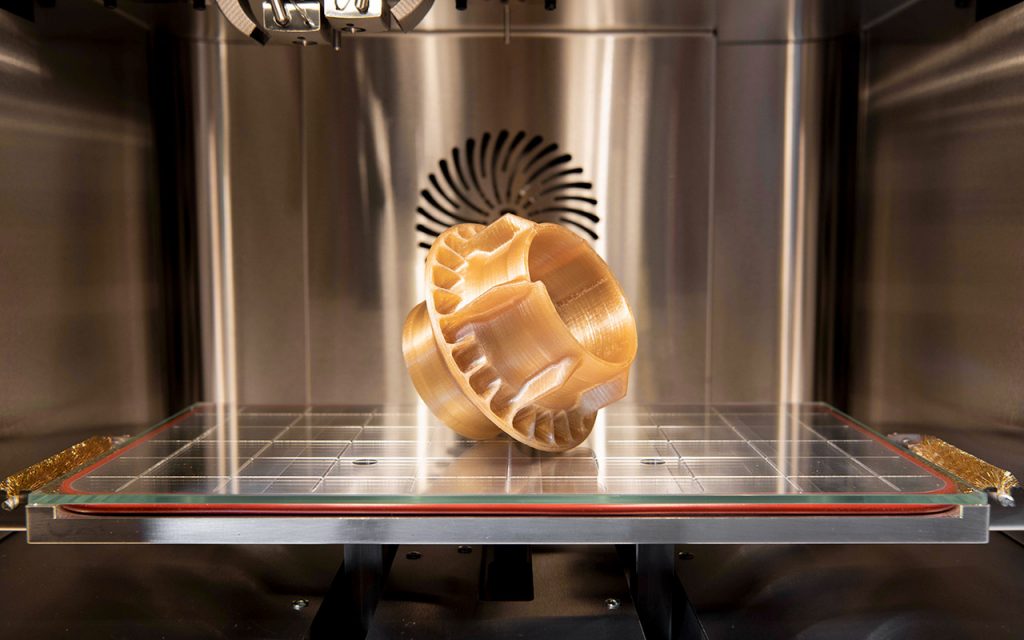
ULTEM 1010 y 9085
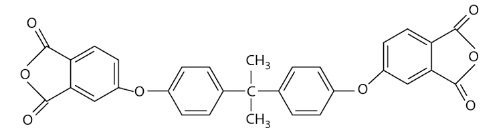
ULTEM es la marca del PEI (polieterimida), un filamento de altas prestaciones producido por SABIC. El PEI ofrece propiedades similares, aunque ligeramente inferiores, al PEEK a un precio significativamente menor. Ambos materiales presentan una excepcional resistencia química, fuerza y rigidez, resistencia al calor a largo plazo, resistencia a la fatiga y estabilidad dimensional. Sin embargo, a diferencia del PEEK, el ULTEM es un material amorfo y, por lo tanto, tiende a mostrar una menor resistencia al calor, a pesar de que tiene una temperatura de transición vítrea de alrededor de 210°C (ULTEM 1010).
Al igual que el PEEK, el ULTEM 1010 también puede ser esterilizado y es autoclavable. Algunos grados también son biocompatibles y están certificados para uso alimentario. Además, el ULTEM 1010 presenta una excelente resistencia química y térmica.
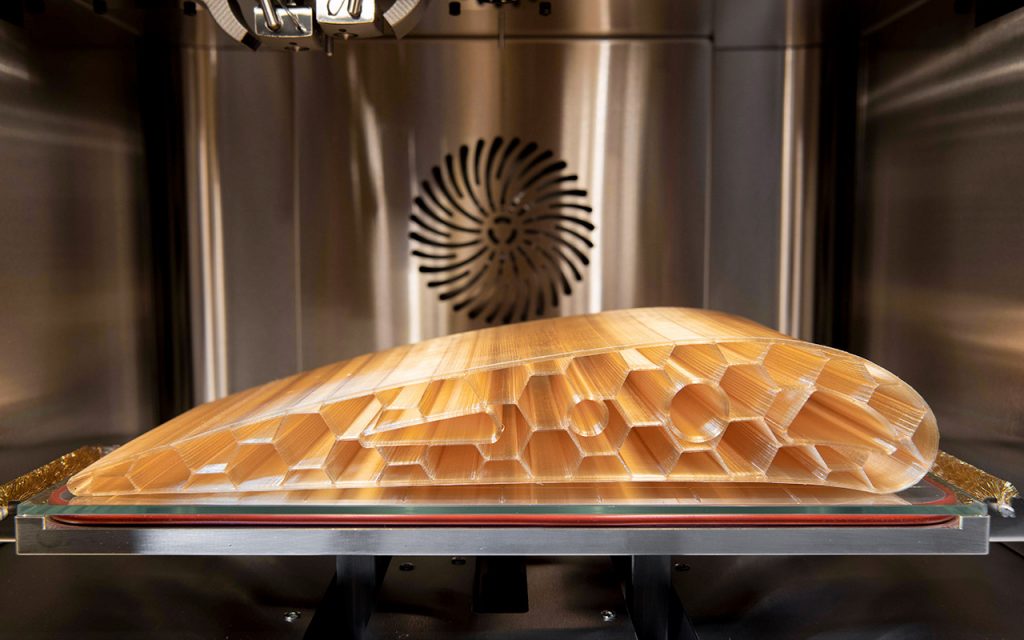
ULTEM 9085 es otra versión de la resina ULTEM producida por SABIC que está disponible para la impresión FDM. A primera vista, el ULTEM 9085 ofrece menor resistencia química y propiedades termomecánicas que el ULTEM 1010. De hecho, el ULTEM 9085 tiene un HDT de unos 153 °C, que es unos 50 °C inferior al del ULTEM 1010. Además, el ULTEM 9085 tiene menor resistencia y rigidez que el ULTEM 1010, aunque esto hace que el primer material sea más tolerante que el segundo. Por otro lado, el ULTEM 9085 ofrece una tenacidad y una resistencia al impacto significativamente mayores que el ULTEM 1010.
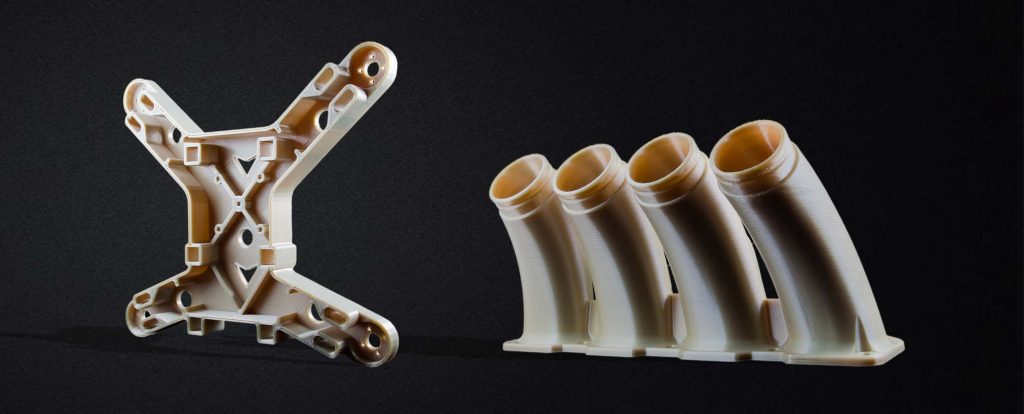
PPSU / PPSF

PPSU / PPSF (Polifenilsulfona) es un filamento de alto rendimiento de la familia PSU (Polisulfona). Las polisulfonas describen los polímeros que contienen una fracción de sulfonilo (O = S = O) en su unidad de repetición. Estos termoplásticos se utilizan a menudo en aplicaciones especiales como sustituto superior de los policarbonatos. Otros polímeros de la misma familia son el PSU (polisulfona), el PPS (polisulfuro de fenilo) y el poli-PSF (bisfenol-A sulfona).
El PPSU es un material amorfo con una temperatura de transición vítrea muy alta (> 230°C) y una temperatura de desviación del calor en torno a 190°C, lo que lo hace ideal para aplicaciones de alta temperatura. El PPSU suele tener una temperatura de funcionamiento elevada (180°C), una gran resistencia al impacto y una gran estabilidad dimensional. El termoplástico también muestra una muy buena compatibilidad química y una alta resistencia a la hidrólisis. Curiosamente, el PPSU también muestra una gran resistencia a la radiación gamma y puede esterilizarse tanto con técnicas de autoclave como de radiación.
PVDF
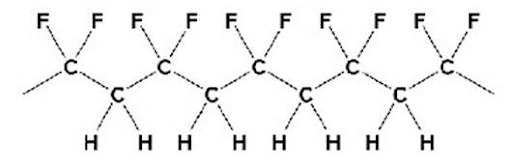
El PVDF (fluoruro de polivinileno) es un termoplástico altamente inerte relacionado con el PTFE (teflón). Los átomos de flúor están estrechamente unidos a los átomos de carbono en la estructura del floupolímero, lo que da lugar a la extraordinaria resistencia química y térmica de este polímero. El PVDF es compatible con una amplia gama de productos químicos, incluidos el petróleo, el gas y los lubricantes, así como los hidrocarburos halogenados, los alcoholes, los ácidos y las bases. Además, el PVDF puede soportar la radiación nuclear y es muy resistente a los rayos UV, la radiación gamma y la oxidación. El PVDF también presenta una alta resistencia mecánica y puede utilizarse de forma continua a temperaturas de hasta 150°C.
Tabla 1: Propiedades mecánicas típicas de los materiales de impresión a alta temperatura, fuente: 3dxtech.com
Material | Resistencia (MPa) | Módulo (MPa) | Alargamiento (%) | Resistencia a la flexión (MPa) | Módulo de flexión (MPa) | Tg (° C) | HDT (° C) |
PEEK | 100 | 3270 | 28 | 130 | 2700 | 143 | 140 |
PEKK | 105 | 3200 | 10 | 134 | 2900 | 164 | 182 |
ULTEM 1010 | 56 | 2500 | 3 | 110 | 2510 | 217 | 208 |
ULTEM 9085 | 54 | 2050 | 3 | 90 | 2170 | 186 | 158 |
PPSU | 55 | 2310 | 3 | 110 | 2215 | 230 | 190 |
PVDF | 51 | 2450 | 25 | 50 | 1800 | 170 | 158 |
Impresión 3D de materiales de alta temperatura
Dado que todos estos materiales tienen un punto de fusión y una temperatura de transición vítrea elevados, la mayoría de las veces se necesitan impresoras especializadas de alta temperatura para imprimir con éxito. La siguiente tabla muestra las condiciones típicas de impresión requeridas para imprimir varios materiales de alta temperatura. Estos valores reflejan las recomendaciones generales para la impresión de materiales de alta temperatura. Sin embargo, las condiciones de impresión dependerán en gran medida de otros factores como la impresora, el material, el tamaño y la geometría de la pieza y también de las propiedades mecánicas esperadas de la pieza impresa, como se comenta a continuación.
Tabla 2: Condiciones típicas de impresión para materiales de impresión de alta temperatura
Material | Boquilla (° C) | Placa de construcción (° C) | Cámara (° C) |
PEEK | 380-420 | 120-160 | > 90 |
PEKK | 365-400 | 120-150 | > 90 |
ULTEM 1010 | 380-420 | > 150 | > 120 |
ULTEM 9085 | 365-385 | > 140 | > 90 |
PPSU | 380-420 | > 150 | > 120 |
PVDF | 250-280 | 70-110 | / |
Cámara calefactada
Una cámara de impresión con calefacción activa es un requisito absoluto para imprimir piezas de tamaño modesto con la mayoría de los materiales de alta temperatura. Como resultado de sus elevados puntos de fusión y temperaturas de transición vítrea, la impresión de materiales de alta temperatura a temperatura ambiente dará lugar a una mala adherencia de las capas, lo que dará lugar a piezas debilitadas. Además, una cámara calentada no sólo ayudará a garantizar la máxima resistencia Z, sino que también ayudará a reducir las tensiones internas y a limitar la deformación durante la impresión. Una cámara calefactada también ayuda a aumentar las posibilidades de éxito de las impresiones de las piezas más grandes.
Cristalinidad
Dado que los materiales semicristalinos, como el PEEK y el PEKK, son semicristalinos, la cristalinidad total de una pieza moldeada puede controlarse mediante el control de la velocidad de enfriamiento del material extruido. Una velocidad de enfriamiento lenta favorece la formación de regiones cristalinas dentro de un material. Por otro lado, las piezas que se enfrían rápidamente tienden a formar un plástico amorfo.
Las piezas amorfas suelen tener menor resistencia química, a la fatiga y al desgaste, pero tienen mejores características de adhesión y buena capacidad de conformación. Por otro lado, las piezas cristalinas tienden a mostrar una fuerza, una resistencia al desgaste y una resistencia química superiores, aunque con características de adhesión inferiores. Por último, los materiales amorfos tienden a ser transparentes, mientras que las partes cristalinas tienden a ser opacas.
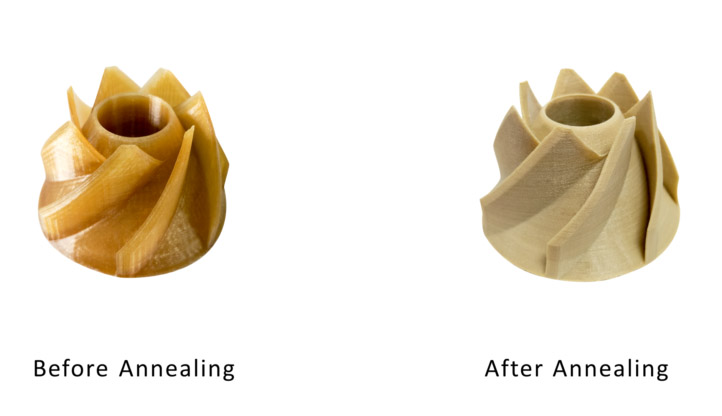
Secado de los filamentos
La mayoría de los materiales de alta temperatura también tienden a absorber agua cuando se exponen a un ambiente húmedo. Por lo tanto, hay que tener especial cuidado en almacenar los filamentos adecuadamente y secarlos completamente cuando sea necesario. Los filamentos que han absorbido agua tienden a producir piezas con propiedades mecánicas y estéticas inferiores.
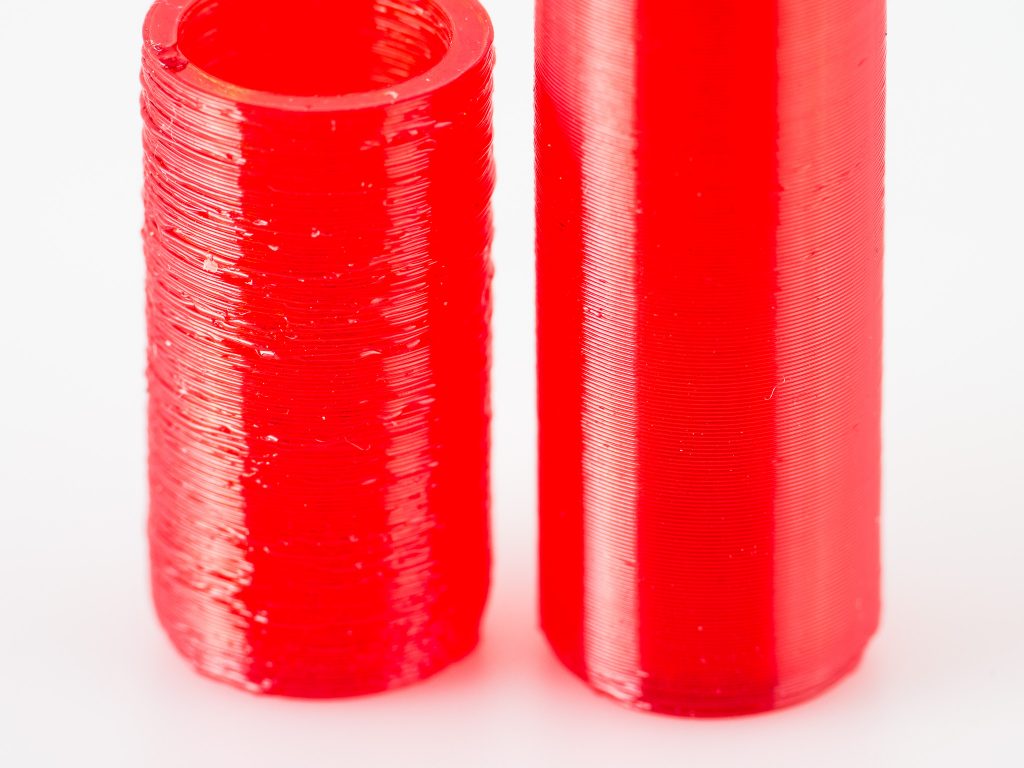
Recalentamiento
Las piezas impresas con materiales de alta temperatura podrían beneficiarse considerablemente del recocido. Este proceso consiste en calentar la pieza hasta una temperatura determinada y luego enfriarla a un ritmo controlado. El recocido sirve para aliviar las tensiones internas en los plásticos amorfos, pero lo más importante es que puede aumentar drásticamente la cristalinidad en los materiales semicristalinos, lo que permite mejorar las propiedades mecánicas. Esto es especialmente importante en el caso de materiales como el PEEK, que a veces se moldea en estado amorfo, ya que esto favorece una mayor adhesión de las capas. Por lo tanto, las piezas se recuecen para aumentar la cristalinidad, ya que las piezas impresas directamente en estado cristalino tienden a mostrar una mala adherencia de las capas.
Primera capa de adherencia

Créditos @magigoo.com